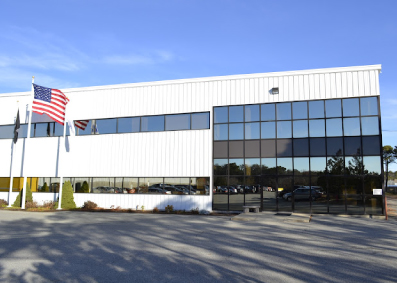
Grays Peak and Valore Ventures’ Acquires SencorpWhite, Expanding its Position as a Global Leader
Grays Peak and Valore Ventures’ ability to deliver end-to-end automation and storage solutions, addressing complex fulfillment and logistics challenges…
NEW YORK, May 28, 2025 The SencorpWhite portfolio adds a powerful group of renowned brands to a growing platform:
- White Systems – A market leader in vertical and horizontal carousels and Vertical Lift Modules (VLMs)
- Ascent Warehouse Logistics – Provider of Warehouse Management Systems (WMS) and Warehouse Execution Systems (WES)
- Accu-Seal and CeraTek – Industry-trusted names in medical, laboratory, and industrial heat sealing technologies
Together, these offerings reinforce Grays Peak and Valore Ventures’ ability to deliver end-to-end automation and storage solutions, addressing complex fulfillment and logistics challenges in retail, manufacturing, healthcare, pharmaceuticals, and industrial sectors.
For decades, SencorpWhite’s solutions have been deployed across thousands of global installations, supported by comprehensive customer services, including technical support, field service, and spare parts. The company’s legacy of engineering excellence, precision manufacturing, and customer-centric design now forms a cornerstone of the portfolios enhanced capabilities.
“The acquisition of SencorpWhite meaningfully enhances our position as a category-defining leader in the automation and material handling industry,” said Scott Stevens, CEO of Grays Peak Capital. “This acquisition complements our existing portfolio—including McMurray Stern, Spacesaver Interiors and Tompkins Solutions—and significantly strengthens our vertical integration strategy, allowing us to serve the full spectrum of customer needs, from secure modular lockers to fully automated fulfillment ecosystems.”
SencorpWhite will continue operating under its trusted brand names, with a renewed focus on scaling innovation and operational excellence. Its heat-sealing technologies under CeraTek and Accu-Seal will remain critical to high-compliance industries such as medical devices, biotech, food, and aerospace packaging, where precision, sterility, and reliability are paramount.
“Partnering with Grays Peak and Valore Ventures opens a new chapter for our company,” said Corey Calla, President and CEO of SencorpWhite. “Their strategic insight, resources, and commitment to innovation will empower us to accelerate product development, deepen customer relationships, and expand our market presence. We are excited to build the future of automation together.”
This acquisition aligns with the long-term vision of Grays Peak Capital and Valore Ventures, to build a world-class platform that unites top-tier integrators, manufacturers, and software innovators into a fully integrated, automation-first enterprise. With an unmatched suite of engineering and implementation capabilities, the portfolio is uniquely positioned to drive the evolution of global supply chains and warehouse ecosystems.
About Valore Ventures
Valore Ventures invests in operating companies and commercial real estate with a focus on long-term value creation. The firm partners closely with management teams to unlock growth and optimize performance, while also redeveloping strategic real estate assets across the United States. Visit https://valore-ventures.com for more information.
Media Contact
Bridget Burkhardt
Vice President
bburkhardt-8013@sencorpwhite.com
(774) 822-0143
About Grays Peak Capital
Grays Peak Capital (www.grayspeakcapital.com) Grays Peak is a global alternative investments firm currently managing assets for a diverse investor base of high-net worth individuals, family offices and institutions. Our portfolio includes multinational brands that have created value by disrupting mature industries and embracing technological innovation.
Using a tiered investment process, we are able invest across the capital structure. We express these investments through our funds focusing on Venture Capital, Private Equity and Hedge Fund.
Our goal is to identify and invest in disruptive industry trends focusing on Consumer and Technology. We target industries and sectors that are undergoing disruptive change typically catalyzed by technology. We invest in seed to late-stage and public companies, focusing on consumer and technology, media and telecom companies.
Contact:
Scott Stevens -CEO
212-506-7050
info@grayspeakcapital.com
https://grayspeakcapital.com/
SOURCE Grays Peak Capital