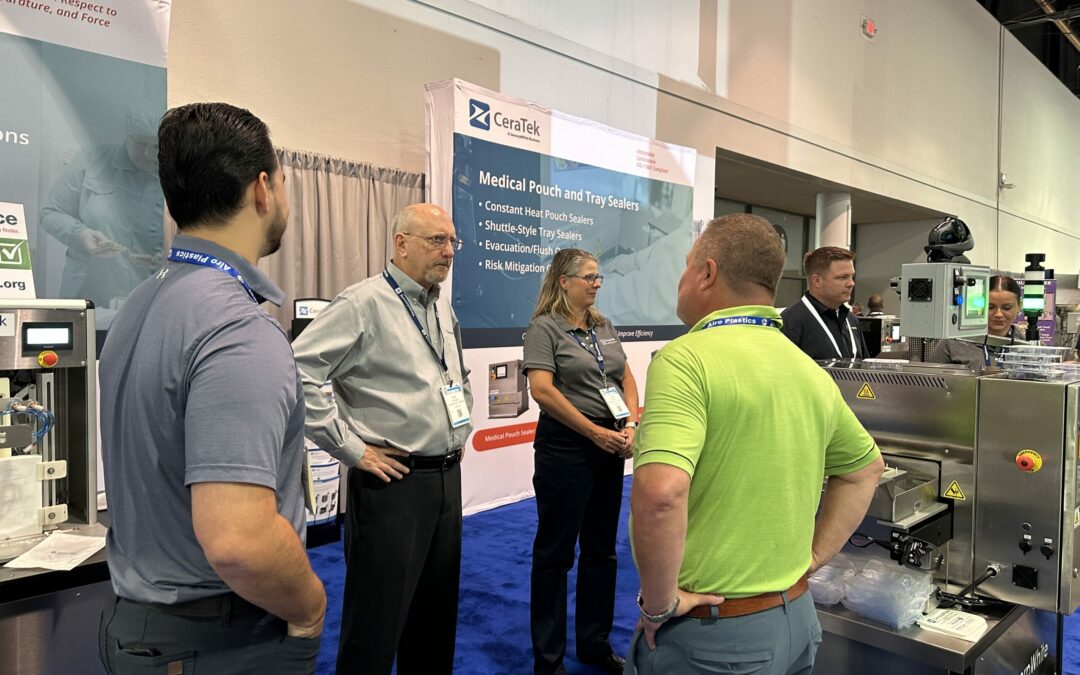
The Medical Tray Sealing Process

What is the medical tray sealing process?
Medical tray sealing involves applying a specific temperature for a specific amount of time under a specific pressure so that the lid and tray materials are bonded together. First, the rigid plastic tray, usually empty, is placed into a tool in the tray sealing machine. Then, an operator manually places the product in the tray and rests the lid stock on top. Next, the tray is shuttled into the tray sealing machine where the correct temperature, time, and pressure are applied. Once the sealing is complete, the tray exits the tray sealer and the operator unloads the finalized sealed package.
Achieving a good bond between the lid and the tray requires an exceptionally flat and parallel sealing platform, as well as the highly regulated and consistent application of temperature and pressure. To achieve a hermetic seal, it is critical for the both the lid and tray to conform and make intimate contact all the way around the perimeter of the tray. That means the tray sealer must accommodate for the inherent variability of lid and tray materials by being accurate and consistent.
The difference between tray sealing and pouch sealing
The process used for tray sealing is similar to the one used for pouch sealing; however, the two processes do differ in significant ways. For example, with pouch sealing, two flexible materials are bonded together. With tray sealing, a flexible material (lid) is bonded to a rigid material (tray). In addition, pouch sealing involves bonding a narrow band across the top of the pouch, while tray sealing involves applying consistent temperature and even pressure over a much wider area. In fact, comparing the average tray versus the average pouch, the amount of seal area is quadrupled. That means tray sealing requires a larger press area and greater control over the application of temperature and pressure.
How medical device tray sealing differs than other types of sealing
The most important difference between medical device tray sealing and other types of sealing is that the materials used for the tray and the lid must be able to be bonded together to create a package that can be sterilized and maintain sterility over the shelf life of the product. In many cases, it is also important that the tray is designed to immobilize the product. Tray sealers used to package medical devices feature very precise systems for controlling time, temperature, and pressure during the sealing process. In fact, this level of accuracy and repeatability is what separates medical device tray sealers from other types of sealers. For packaging equipment to be even considered capable of sealing medical trays, it must be validatable, meaning that the sealer must be verified to provide the same results repeatedly with very little to no deviation.