Validating Heat Sealers
Validation of heat sealers using IQ, OQ, and PQ
Heat sealers must be validated before they can be used in production. This validation is a three-phase process.
The first phase is the IQ, which stands for installation qualification. During the IQ, the medical device manufacturer verifies that the heat sealer was built to spec, has the needed utilities, and was installed properly.
The second phase is the OQ, or operational qualification. For the OQ, the medical device manufacturer must walk through all the control processes of the heat sealer and verify that it operationally functions every time as it should. The temperature control, pressure control, time control, recipe control, alarms and all other operational aspects must be verified.
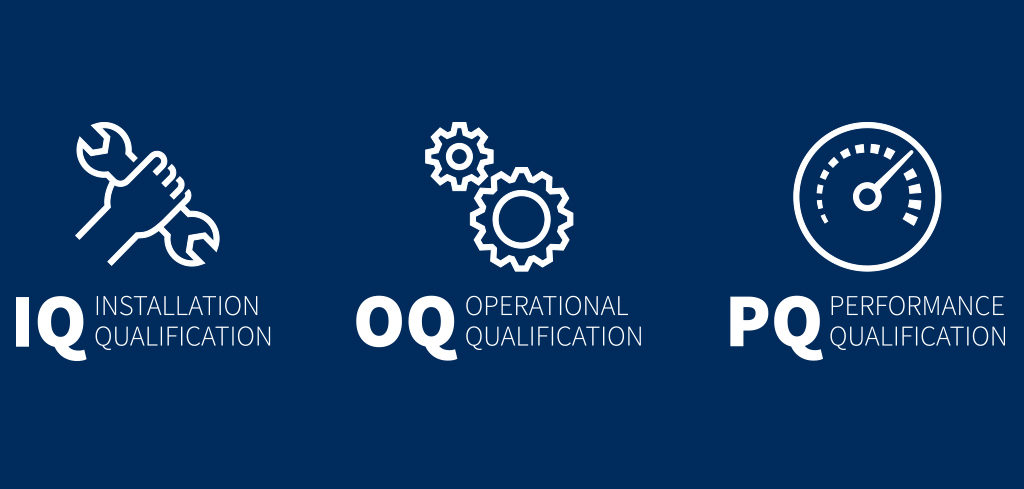
The final phase is process qualification, or PQ. The PQ phase involves observing the heat sealer in combination with the medical pouch it’s going to seal, i.e., the actual heat sealing process. The IQ and the OQ are focused on the heat sealer itself. The PQ phase verifies that the heat sealer is delivering a repeatable process and that the medical pouch is sealing in a repeatable fashion. It confirms that the output is what it’s supposed to be.
Any heat sealer used for medical pouch sealing should be ISO 11607-compliant. ISO 11607 is a guidance document that is used to define many different aspects of sterile packaging. For example, for a piece of sealing equipment to be ISO 11607-compliant, it must have the ability to verify and alarm temperature, pressure, and time.
FDA approval of medical pouches
Just as medical products require FDA approval, medical packaging must also be FDA approved. Medical device manufacturers need to have their manufacturing and packaging processes regularly audited to ensure that they are using the proper equipment and that it has been validated and maintained properly. The FDA offers approval guidelines for medical manufacturers to follow, but it does not provide instructions.
The types of heat sealer options
Today’s heat sealers can come equipped with options that help with compliance and risk mitigation. Traditionally, medical pouch sealing has been mostly a manual operation. However, more and more medical device manufacturers are implementing automation and other features to minimize operator error and mitigate other risks.
For example, some heat sealers are not enabled to cycle until the product which is put into the package is confirmed by weight. Others are equipped with barcode readers, vision cameras, or other sensors that detect certain markings on a pouch to verify that it has been positioned correctly for sealing. The cycle will only begin if the medical pouch is properly oriented and located. In some cases, heat sealers come equipped with alarms to alert the operator of errors and that a pouch needs to be put into a quarantine bin before the next cycle can start. They can also have outputs designed to control conveyors that move a pouch to the next process based on whether or not there was a good or a bad cycle.
Features for printing are also becoming more popular. For example, inkjet printers or embossing type systems can be added to continuous band or a rotary band sealers so that the medical pouches are printed on as they are sealed. Embossers can also be added to jaw type heat sealers to emboss a fixed imprint into the pouch.
In addition, other ancillary equipment can be added to heat sealers to help operators work more efficiently. For instance, some heat sealers have a pouch opening system that will pull a pouch out of a magazine and present it to the operator in an open format. After the operator places the product into the pouch, the pouch opener releases the package so that the operator can seal it. Since operators working in a clean room are typically gloved, this type of pouch opening system can significantly increase throughput. Efficiency can also be improved using static elimination options, which range from an overhead ionizing fan blowing down on the assembly area to reduce the static field to static elimination chambers for the medical pouches to pass through.