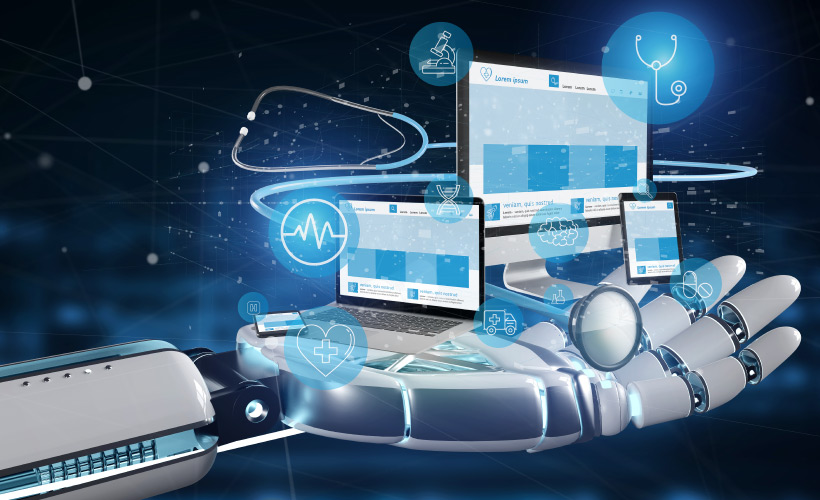
What role does automation play in risk mitigation for medical device packaging?
Automation provides unique opportunities for the medical device industry. First and foremost, automating a packaging process removes the operator from the process, eliminating the risk of human error, which is the greatest risk. When a packaging process is automated, the machine is programmed to complete a particular set of steps in a particular order. That process can be validated, ensuring a repeatable and reliable process.
The downside of automation is it is significantly more challenging to validate. Validating a piece of automation takes repeated testing and trial and error, as engineers introduce variables to impact the process in different ways. By contrast, a human operator is able to look at a package and decide that it doesn’t look quite right (without knowing the reason why). In other words, they can assess variables that may have not been tested.
Risk mitigation is very frequently just trying to engineer out the distractions that we know operators experience and where there might be gaps in that process where a distracted operator might make a mistake. This makes automation a good fit for longer runs, longer lifecycle products, where there would be a return on the upfront investment needed to validate the process.
Likewise, automation may be optimal for a high value product that has a very complex packaging process with many risk factors. In this case, the validation process associated with automation may be worthwhile to ensure that the high value product does not have the opportunity for risks related to a human process.
Why is automation such a good fit for rotary band sealers, continuous sealers, and pouch filling devices?
Using automation with rotary band sealers, continuous sealers, and pouch filling devices is becoming increasingly commonplace because it can increase throughput and mitigate risks caused by human error.
Automation can be used for packaging, for inspection and counting of the finished packages, and for segregating of finished packages by whatever parameter is required. With automation, operators do not have to worry about making mistakes. The entire process is handled automatically. If errors occur, they can be detected by sensors, and the incorrect packages are diverted to a reject bin. Alarms notify operators if any of the automated processes fail.
What are the future trends in medical device packaging risk mitigation?
CeraTek is committed to identifying areas for improvement and then implementing these improvements to benefit our customers. To that end, we are currently working on integrating our heat sealers with load cells that measure the amount of force being delivered to the seal area. This will ensure that the sealing die is closing fully and has delivered the correct amount of force. It could also offer an opportunity to start and end the dwell time off of a force window that is saved in the recipe.
These features will allow the heat sealer to maintain the desired seal pressure and risk mitigation features, while still controlling and alarming for the correct input pressure. We are also actively pursuing an automated seal inspection for our pouch sealer. This would be a system through which the sealed pouches automatically index for inline nondestructive seal inspection and it would satisfy the medical device industry requirement for Container Closure Integrity Testing (CCIT).
More and more medical device manufacturers are requiring CCIT systems in their sealing equipment to ensure that every package that comes out of the heat sealer is inspected according to a programmed set of inspection pass-fail requirements. In automated environments, it is not subject to manual inspection by an operator, who may or may not make the correct judgment call, or who may or may not get distracted.
What’s important to look for in a heat sealer manufacturer?
When evaluating heat sealer manufacturers, it is essential to find one that fully understands your particular project and has experience solving similar challenges. CeraTek focuses on solving problems, not simply selling machines. We partner with our customers and work together for shared success. Our goal is to provide our customers with the packaging solutions they need to get their products safely, reliably, and efficiently to the people who need them.